The Bessemer steel process, named after its inventor Sir Henry Bessemer, was a groundbreaking method for producing steel in the mid-19th century. This process revolutionized the steel industry by making it possible to mass-produce steel, which had a significant impact on various sectors, including construction, transportation, and manufacturing. The Bessemer process involved blowing air through molten pig iron to remove impurities, resulting in a stronger and more durable material. Here, we'll explore 5 key aspects of the Bessemer steel process and its significance.
Key Points
- The Bessemer process was the first method to produce steel efficiently on a large scale.
- It involved blowing air through molten pig iron to remove impurities like carbon and silicon.
- The process significantly reduced the production time and cost of steel, making it more accessible for various applications.
- Despite its revolutionary impact, the Bessemer process had limitations, including the production of steel with varying quality and the need for high-quality raw materials.
- The development of alternative steel production methods, such as the open-hearth furnace and basic oxygen steelmaking, eventually replaced the Bessemer process due to their ability to produce higher-quality steel more efficiently.
Introduction to the Bessemer Process

The Bessemer process was patented in 1855 by Sir Henry Bessemer, an English engineer and inventor. Before this innovation, steel production was a labor-intensive and expensive process that involved folding and hammering the metal to remove impurities. The Bessemer process simplified this by using a Bessemer converter, a large, egg-shaped vessel lined with refractory material, to blow air through the molten pig iron. This air blast removed impurities like carbon and silicon, resulting in a higher quality steel product. The process could produce up to 25 tons of steel in a single batch, significantly increasing production efficiency and reducing costs.
Chemical Reactions Involved
The Bessemer process relied on a series of chemical reactions to purify the pig iron. When air was blown through the molten metal, it reacted with the impurities to form slag, which could then be removed. The reactions involved the oxidation of carbon, silicon, and manganese, among other elements. For instance, the reaction between carbon and oxygen formed carbon dioxide, a gas that could be released, thereby reducing the carbon content of the steel. This process allowed for the production of steel with lower carbon content, making it stronger and more versatile than pig iron.
Element | Reaction | Result |
---|---|---|
Carbon | C + O2 → CO2 | Carbon dioxide gas released, reducing carbon content |
Silicon | Si + O2 → SiO2 | Silicon dioxide formed, contributing to slag |
Manganese | Mn + O2 → MnO2 | Manganese dioxide formed, influencing steel properties |

Impact and Limitations of the Bessemer Process
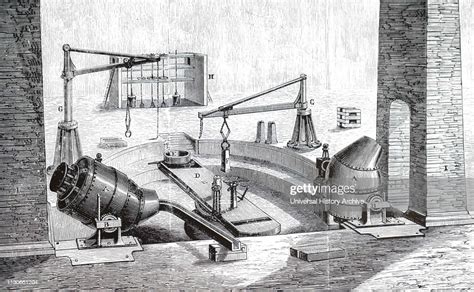
The Bessemer process had a profound impact on the steel industry, enabling the widespread use of steel in construction, railways, and shipbuilding. However, it also had several limitations. One of the main challenges was the variability in the quality of the steel produced, which depended on the quality of the pig iron used as the raw material. Additionally, the process required the raw material to be relatively low in phosphorus and sulfur, as these elements could not be removed by the air blast. These limitations led to the development of alternative steel production methods, such as the open-hearth furnace and basic oxygen steelmaking, which could produce steel of more consistent quality and with greater efficiency.
Evolution of Steel Production Technologies
Following the Bessemer process, several other steel production technologies were developed to address its limitations. The open-hearth furnace, for example, used a regenerative furnace to melt and purify the steel, allowing for better control over the chemical composition of the final product. Later, the basic oxygen steelmaking process was introduced, which used pure oxygen instead of air to reduce the impurities in the steel, resulting in a faster and more efficient process with higher-quality steel output. These advancements have continued to evolve, with modern steel production involving highly sophisticated technologies to produce a wide range of steel grades for various applications.
What was the primary innovation of the Bessemer steel process?
+The primary innovation was the use of a blast of air to remove impurities from molten pig iron, significantly simplifying and speeding up the steel production process.
What were the main limitations of the Bessemer process?
+The main limitations included the variability in the quality of the produced steel, the need for high-quality raw materials, and the inability to remove certain impurities like phosphorus and sulfur.
How did the Bessemer process influence the development of subsequent steel production technologies?
+The Bessemer process laid the groundwork for later innovations by demonstrating the potential for large-scale steel production. Its limitations drove the development of new technologies, such as the open-hearth furnace and basic oxygen steelmaking, which overcame these limitations and further improved steel production efficiency and quality.
In conclusion, the Bessemer steel process was a pivotal innovation in the history of steel production, marking the transition from small-scale, labor-intensive methods to large-scale, industrial processes. While it had its limitations, the Bessemer process paved the way for subsequent technological advancements that have enabled the modern steel industry to produce a wide range of high-quality steel products efficiently and cost-effectively. Understanding the historical context and technical aspects of the Bessemer process provides valuable insights into the evolution of steel production and its ongoing impact on various industries and societies worldwide.