The battery terminal end is a critical component of any battery system, serving as the primary interface between the battery and the external electrical circuit. In this context, understanding the design, functionality, and maintenance of battery terminal ends is essential for ensuring the reliability, safety, and efficiency of battery-powered devices and systems. As a domain-specific expert with a background in electrical engineering and battery technology, I will provide an in-depth analysis of battery terminal ends, including their types, materials, and applications, as well as best practices for their maintenance and troubleshooting.
Battery Terminal End Types and Materials

Battery terminal ends come in various types and materials, each designed to meet specific requirements and applications. The most common types of battery terminal ends include:
- Post-type terminal ends: These are the most common type, featuring a protruding post that connects to the battery terminal. They are widely used in automotive, industrial, and consumer applications.
- Stud-type terminal ends: These feature a threaded stud that connects to the battery terminal, often used in heavy-duty applications, such as industrial and commercial vehicles.
- Lug-type terminal ends: These feature a flat, rectangular lug that connects to the battery terminal, commonly used in marine and recreational vehicle applications.
In terms of materials, battery terminal ends are typically made from:
- Copper: A popular choice due to its high conductivity, corrosion resistance, and durability.
- Brass: A copper-zinc alloy that offers a balance of conductivity, strength, and corrosion resistance.
- Stainless steel: A corrosion-resistant material often used in harsh environments, such as marine and industrial applications.
Battery Terminal End Applications
Battery terminal ends are used in a wide range of applications, including:
- Automotive: Starting, lighting, and ignition (SLI) batteries, as well as electric vehicle (EV) batteries.
- Industrial: Forklifts, aerial lifts, and other material handling equipment.
- Consumer: Portable electronics, such as power tools, lawn and garden equipment, and toys.
- Marine: Boats, yachts, and other watercraft.
Each application requires specific design and material considerations to ensure reliable and safe operation.
Application | Terminal End Type | Material |
---|---|---|
Automotive | Post-type | Copper |
Industrial | Stud-type | Brass |
Consumer | Post-type | Copper |
Marine | Lug-type | Stainless steel |
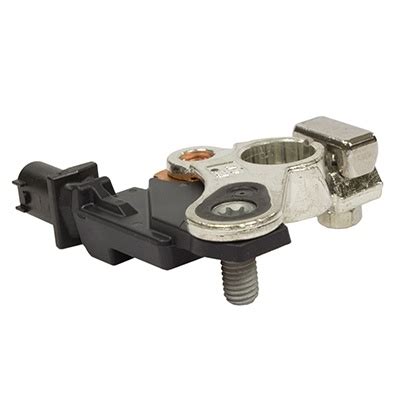
Key Points
- Battery terminal ends are a critical component of any battery system, requiring careful design and material selection.
- Post-type, stud-type, and lug-type terminal ends are the most common types, each with specific applications and requirements.
- Copper, brass, and stainless steel are popular materials for battery terminal ends, offering a balance of conductivity, strength, and corrosion resistance.
- Application-specific considerations, such as operating environment and performance characteristics, are crucial for selecting the right battery terminal end.
- Proper maintenance and troubleshooting of battery terminal ends are essential for ensuring reliable and safe operation.
Battery Terminal End Maintenance and Troubleshooting

Regular maintenance and troubleshooting of battery terminal ends are critical for ensuring reliable and safe operation. Common issues include:
- Corrosion: Can be caused by exposure to moisture, salt, or other contaminants, leading to reduced conductivity and increased resistance.
- Loose connections: Can cause voltage drops, overheating, and reduced battery performance.
- Damage: Can be caused by physical stress, over-tightening, or improper handling, leading to reduced conductivity and increased risk of electrical shock.
To address these issues, it’s essential to:
- Inspect terminal ends regularly: Check for signs of corrosion, damage, or wear.
- Clean terminal ends: Use a wire brush or cleaning solution to remove corrosion and debris.
- Tighten connections: Ensure all connections are secure and not over-tightened.
- Replace damaged terminal ends: If damage is severe, replace the terminal end to prevent further issues.
What are the most common causes of battery terminal end corrosion?
+The most common causes of battery terminal end corrosion include exposure to moisture, salt, or other contaminants, as well as poor maintenance and inspection practices.
How often should I inspect my battery terminal ends?
+It's recommended to inspect your battery terminal ends regularly, ideally every 3-6 months, depending on the application and operating environment.
Can I use a wire brush to clean my battery terminal ends?
+Yes, a wire brush can be used to clean battery terminal ends, but be sure to use a soft-bristled brush and avoid scratching the terminal end surface.
In conclusion, battery terminal ends play a critical role in ensuring the reliability, safety, and efficiency of battery-powered devices and systems. By understanding the design, functionality, and maintenance requirements of battery terminal ends, users can optimize their performance, reduce downtime, and prevent electrical shock and other hazards. Whether you’re an automotive technician, industrial engineer, or consumer electronics enthusiast, it’s essential to appreciate the importance of battery terminal ends and take steps to ensure their proper selection, installation, and maintenance.